European industrialists have decided to create a powerful battery industry to support the redeployment of its automotive industry towards electric vehicles, with the support of governments and the European Union. But the 30 or so planned gigafactories will depend on imports of refined raw materials and components to make batteries. In addition, Asian manufacturers will have a strong presence in these future factories. The European objective of strategic autonomy could be complicated to achieve, regardless of the policies implemented.
____
Europe is witnessing the aggressive development of a lithium-ion battery industry. It is expected to reach 25% of the world’s production capacity by 2030, a target set by Europe, with more than 30 gigafactories[1] by that date, including four or five in France. The number of projects has risen from eight at the end of 2018 to more than 20 by 2021. Of the 22 projects announced, 15 have been seriously launched. They should create a total production capacity of 500 GWh/year of batteries in 2030.
One could imagine that these developments will be carried out by European manufacturers who are strongly committed to the global competition in green technologies (electric vehicles, batteries, electrolysers, etc.). And all this with the support of the European Union, which has finally abandoned its refusal of any industrial policy and would like to build its strategic autonomy, which it talks about a lot by identifying the risks of dependence on critical materials. But this is not the case. The questions of industrial policy, dependence and sovereignty have some difficulty in being integrated into the European grammar. Little is being done to address the dependence of the future battery industry at all levels of its supply chain. And, in the name of respecting the rules of competition and free trade, this nascent industry is not really protected.
1. The ambiguous development of battery factories in Europe
The nascent battery industry, associated with that of electric vehicles, is and will be very exposed to competition from foreign producers, especially Chinese. They not only have the advantage of being able to lead the way, but also have significant competitive advantages, including control of their supply chain for minerals and components, as well as economies of scale due to the strength of their domestic market. The nascent European industry seems condemned to play second fiddle. A significant part of the factories being built in Europe belong to Asian players and competitors. And nothing is being done to preserve national and European interests.
The development of gigafactories in Europe leaves a large space for Asian competitors attracted by the future demand of car manufacturers switching to electric vehicles. These are the South Koreans, LG Chem, Samsung SDI and SKI Innovation and the Chinese CATL Innovation and Farasis for four plants in Germany and Envision AESC for a plant with Renault in France. The three South Koreans have chosen to set up their plants in Eastern Europe, the first in Poland and the others in Hungary (Figure 1).
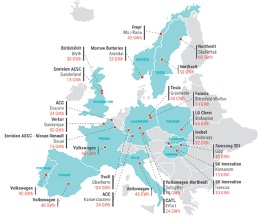
Figure 1. Location of the main battery plants and their maximum annual production capacity under development in Europe – [Source: © Beeker E., 2022, Gigafactories for batteries: Europe takes up the challenge. Focus Edenmag°15]
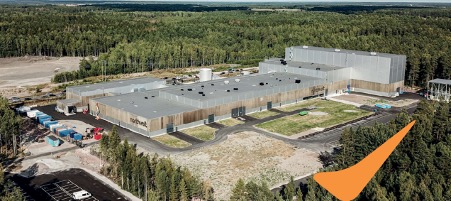
Figure 2. NorthVolt plant in Skelleftea, Sweden – [Source: © Beeker E., 2022, Gigafactories for batteries: Europe takes up the challenge. Focus Edenmag°15]
2. The various constraints on entry into the battery manufacturing business
As in any type of industry where mass production and process knowledge save money, new market contenders experience entry constraints.
2.1. The long learning curve for entrants
It will be difficult for cell producers entering the market to quickly reach the high quality standards of manufacturing in the supply chain of electric vehicles in the global market, whether in the refining of mineral materials (cobalt, lithium, graphite) or in the manufacturing of cathodes and anodes. The learning difficulties of Chinese producers during their emergence between 2015 and 2020 illustrate the problem.
In 2017, they were still unable to produce batteries of the quality of Korea’s LG Chem or Japan’s Panasonic. CATL, however, stood out from the rest in its ability to catch up with this technology gap.
It quickly became the preferred supplier of automobile manufacturers in China and was able to reduce its production costs. Panasonic, which was the leader until recently and to which Tesla turned to develop its gigafactory in the United States, has itself had great difficulty in mastering this change of scale.
More generally, although there are many projects, many future manufacturers will not immediately reach the standards required to supply the electric vehicle market. Cell producers face multiple challenges in scaling up cell plant production above 20 GWh. Overcoming them may take a long time, according to experts at Benchmark Minerals Intelligence (Moores, 2021).
2.2. Additional constraints imposed by Europe
European cell producers will also be forced from the mid-2020s to have a share of cathode material sourced from recycled sources, according to obligations imposed by the 2006 European Battery Directive. The European legislation, which is always looking for the best environmental practices, imposes quality and environmental performance requirements for the supply of minerals, as well as for the processing of raw materials. The possibility of sourcing recycled materials is a major issue for the European industry in terms of refining materials for recycling and their reuse. This will result in the need to master and develop new manufacturing processes and to absorb additional costs. This may be a technological and even economic advantage in the long run, but it will be a constraint on competitiveness.
3. The different dependencies in the supply chain
As they do not necessarily have all the technological building blocks on their territory, the countries of the European Union are dependent on other countries in the world for their supply chain.
3.1. Dependencies for cell minerals
Benchmark Mineral Intelligence (BMI), which makes forecasts focused on cathode materials, including nickel-cobalt-manganese (NCM) “chemistry,” predicts that European demand for graphite will increase 18.9-fold between 2019 and 2029, 18.9-fold for lithium, 26-fold for nickel, 8.6-fold for manganese, and 9.7-fold for cobalt (Figure 3). Demand growth in Europe will exceed that of other regions of the world, due to ongoing investments.
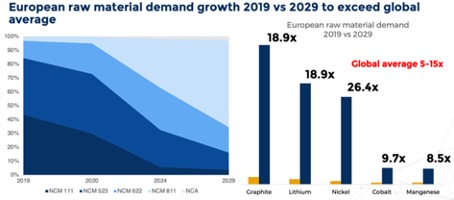
Figure 3. Materials demand projection for the 2020 decade – [Source: © Moores S., 2021, The global battery armsrace: lithium-ion gigafactories and theirsupplychain. Oxford Energy Forum. February 2021: ISSUE 126. p.26-30]
3.2. The European refining industry for critical materials does not exist
The availability of raw materials and materials refining equipment is a major bottleneck to establishing a secure supply chain for the European battery industry. It exposes Europe to market stresses that result from increased long-term purchases by cell manufacturers and automakers in anticipation of their needs. Dramatic price increases for cobalt, lithium and graphite are evidence of this problem.
The EU is dependent on refining activities, even for materials mined domestically, simply because there is no industrial processing capacity at all. Cobalt mined in Europe, especially in Finland, is processed abroad and then re-imported. Similarly, lithium ore is mined in Portugal, which is currently the main European producer with 1,200 tons per year. This country has plans to build a refining plant if local opposition is not too strong. It should be noted that, as with rare earths, the Chinese industry cannot be counted on as an eternal supplier of cobalt or lithium refining. It could one day turn off the export tap not out of geostrategic interest, but to meet its own needs. The risk would be real by 2025, according to analysts.
3.3. Dependence on components
A battery pack is an assembly of modules that contain cells (Figure 4). The cells determine a large part of the pack’s performance. Cell design and manufacturing are at the heart of the international battery technology competition. The basic components of a battery cell are the anode, the cathode (whose dominant chemistry is nickel manganese cobalt (NMC)) and the electrolyte.
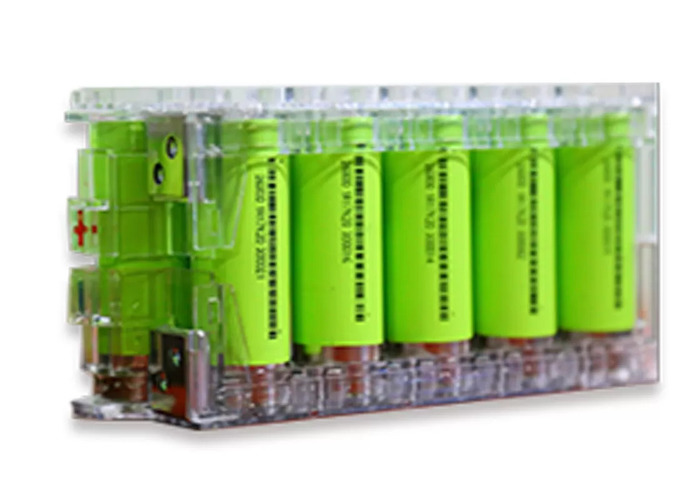
Figure 4. NMC battery cells – [Source: http: //french.libatterypacks.com/quality-13247784-26800-6200mah-nmc-battery-cells]
BASF has two component plant projects in Finland and Germany, but it is still an industrial gamble to be able to compete with the high quality, lower cost production in Asia. The cathode business is capital-intensive. It requires significant long-term investments that generate only modest margins. In addition, new entrants need years of experience to produce high quality cathode materials, particularly for automotive applications where stringent safety standards must be met.
4. The contrast of the Chinese success story
China’s battery industry enjoys many competitive advantages, starting with economies of scale in its domestic market, the world’s largest electric vehicle market, and full control over its raw material supply chain. China has several global leaders, such as CATL, Envision and electric vehicle manufacturer BYP, which were able to compete with the most advanced Asian groups, namely Panasonic (Japan) and LG Chem in South Korea, by the late 2020s.
This industrial domination goes further and extends to the manufacture of key battery cell components. The Chinese industry produced 83% of the anodes and 61% of the cathodes manufactured in the world in 2019. Similarly, it manufactured 73% of the cells that represent about 30% of the cost of a battery that same year (Laboué, 2020).
Chinese companies also control much of the production of key minerals for lithium-ion batteries. China alone accounted for 65% of global production of natural graphite in 2019, the key component for anode production in current generations of batteries (Figure 5). Chinese players are also securing their supplies of minerals not available on their soil by setting up operations abroad. For example, they have bought eight of the 14 cobalt mines in the Democratic Republic of Congo (DRC). They have concluded major supply contracts with lithium ore producers in Australia, Chile and Argentina. China is also at the heart of the commodity refining industry. The country has 80% of the world’s capacity to process battery minerals, including lithium and cobalt.
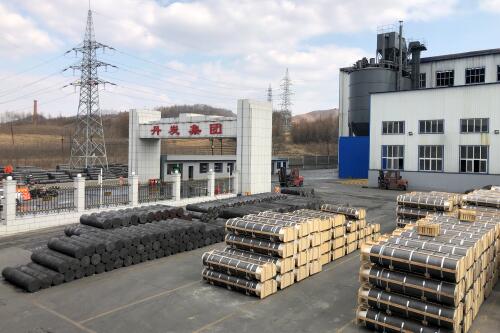
Figure 5: Chinese graphite production plant – [Source: © Dan Carbon – https://www.dancarbon.com/q/graphite-electrode/157.html]
5. European and national industrial policies
The European Union, under pressure from several Member States concerned about the threat to the automotive industry, has decided to enter the battery race as it has in several other cutting-edge fields (quantum computing, artificial intelligence, biotechnology, nanotechnology, among others).
5.1. A difficulty in having a common industrial policy
With its DNA of absolute non-interventionism, Europe has refused until now to adopt a coordinated industrial policy. One of the reasons for this is the rivalry between European firms, as can be seen in the defense and digital industries. It has even often sought to dismantle national champions in the name of free and undistorted competition. But it has finally acquired some means of industrial policy, in particular the Programs of Common Economic Interest (PIIEC), better known as European alliances (or the Airbus of industry), by derogating from the principle of non-intervention to open up the possibility of allocating subsidies at the European level, and also at the level of the States, without major control by the Commission. They offer easier and quicker access to the various forms of aid that can support investment projects: aid from national governments with an accelerated examination of their compatibility with maintaining fair competition on the European market, and aid from European funds.
The principle of alliances is to create intra-European value chains by encouraging the creation of European consortiums with private and public players, laboratories and industrial companies. But they do not close the door to partnerships with foreigners, or to external participation in industrial projects that would be supported in the framework of an alliance.
The European Commission launched a European Battery Alliance (EBA) in 2017 to build an integrated value chain on European soil. Two projects have been approved and launched, one in late 2019 worth €3.2 billion, which brings together seven member states and 17 companies; the other in January 2021 worth €2.9 billion, which is led by TotalEnergies and Stellantis. The latter brings together 42 companies from 12 member countries with the aim of developing the solid state battery. 20 billion in funding, including 6 billion in public funding.
5.2. The refusal to erect protections against foreign competition
It remains to be seen whether the AEB projects will give European companies a decisive advantage in avoiding Asian domination. It is likely that they will help to avoid missing out on the next generation of batteries, namely solid state batteries. They will probably also allow the development of processes to facilitate the recycling of battery materials.
But unlike in Asia and the United States, these new industrial policy tools do not protect against foreign competition and, more importantly, are not designed for it. As mentioned, the principle of alliances does not close the door to the involvement of foreign manufacturers in R&D activities. Similarly, while it facilitates the subsidization of gigafactories and component factories, it does not prohibit the subsidization of factories owned by non-European players. In Germany, for example, the 3 billion euros of aid allocated to the installation of gigafactories benefitthe factories of Tesla and the Chinese companies CATL and Farasis.
The resources deployed in Europe are inferior to those used by China and the United States in every sector of innovation. Chinese manufacturers thrive in a vast domestic market that remains largely inaccessible to foreigners. For example, they require all domestic and foreign car manufacturers to use batteries made in China. In the United States, the Democratic administration is in the process of reserving subsidies for the purchase of electric vehicles solely to vehicles equipped with batteries assembled and manufactured in the country. In addition, manufacturers in these countries are not required to use recycled materials.
6. What role do policies play in strategic materials?
Still with the objective of strategic autonomy, Europe has also adopted a policy on strategic materials, including lithium, cobalt and nickel (Figure 6). In September 2020, the Commission presented an action plan on critical raw materials for 2030 and 2050.
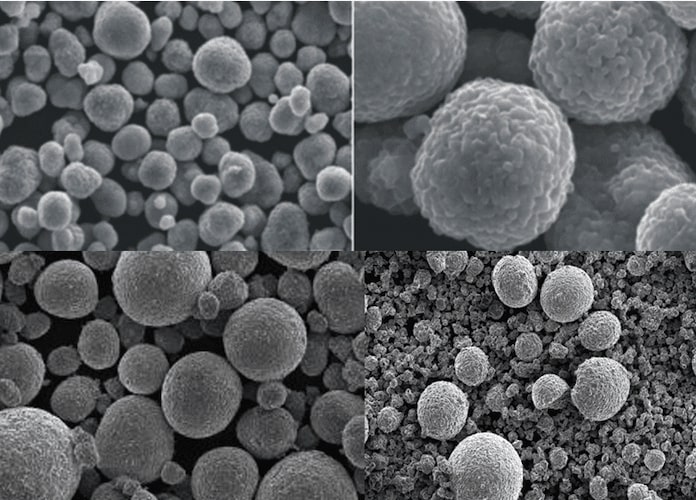
Figure 6. Lithium nickel cobalt aluminium oxide – [Source: © Watson Noke Scientific – 193214-24-3 LITHIUM NICKEL COBALT ALUMINIUM OXIDE (NCA) – Watsonnoke Scientific Ltd]
The first axis is the development of European production. The Commission has launched an inventory of mining and refining projects in the EU that can be operational by 2025. These include cobalt, lithium, natural graphite and nickel. But this response is immediately constrained by the strong local opposition to mining projects, such as those for lithium and rare earths in Portugal (Covas de Barroso) (Figure 7), Spain (Càceres in Extremadura), Sweden (Nora Kârr), Serbia (Jadar), and France (Tréguennec in Finistère, Montebras in Creuse, and Beauvoir in Allier).
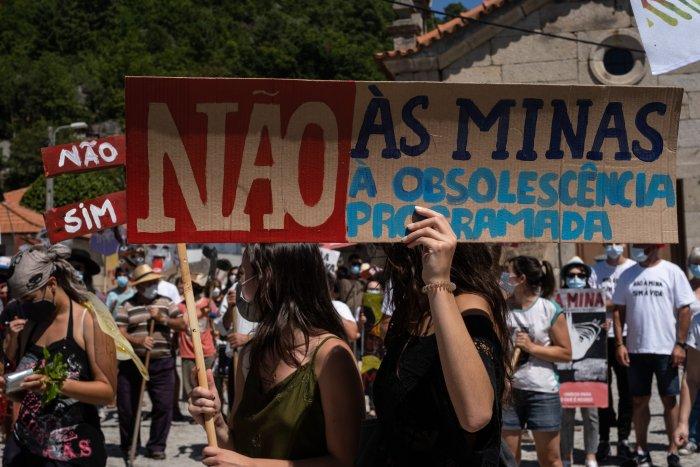
Figure 7. Opposition to the Covas de Barroso mining project in Portugal – [Source: © Infolibertaire.net – https://www.infolibertaire.net/portugal-covas-de-barroso-le-plus-grand-projet-dexploitation-de-lithium-deurope/]
If we can expect a certain security of supply for the EU with such partnerships, it is doubtful that this will solve all the problems posed by this dependence, particularly in terms of refining materials. The European Union is not a geopolitical power. We know what happened to the effectiveness of the Europe-oil exporting countries dialogue that the EEC had tried to establish in the past.
7. The role of national actions
The French government, concerned about these problems, wanted to complement the European approach with a specifically French reflection on “Securing the supply of mineral materials” for the battery and renewable energy industries and for the digital sector, by requesting a report that was submitted to it by Philippe Varin, its rapporteur, in January 2022 (Figure 8). France has decided to take action itself in various directions in addition to those of the EU, in order to serve the country’s own national interests more directly, to move away from intra-European rivalries, from the pernickety application of competition rules and from dependence on an ineffective European diplomacy.
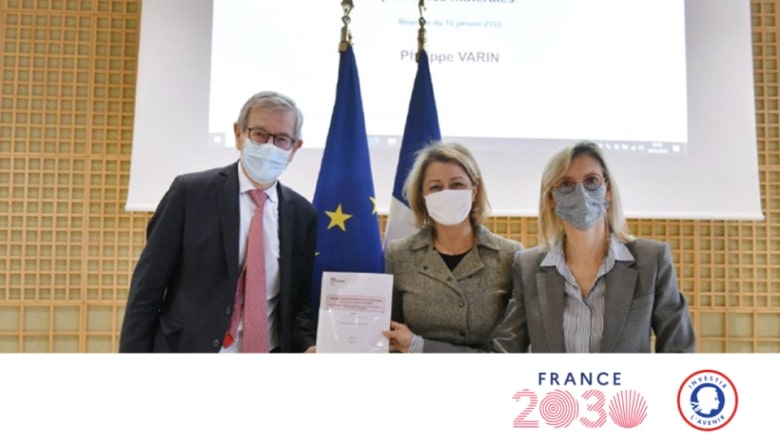
Figure 8. The Varin report submitted to ministers Barbara Pompili and Agnès Pannier-Runacher – [Source: © Mineralinfo – https://www.mineralinfo.fr/fr/actualite/actualite/france-2030-rapport-varin-sur-securisation-de-lapprovisionnement-matieres]
Governments need to explore the potential of locally available resources (especially lithium, nickel and cobalt) and processing capabilities to identify potential supply bottlenecks. They can facilitate collaboration within the value chain through industry forums and create and fund research and educational institutions to develop talent and advance technology. Philippe Varin recommends that the French government put in place:
- a public-private investment fund to secure the supply of critical metals for the three battery gigafactories planned to date on French soil; this fund will be able to take minority positions with experienced miners;
- two industrial platforms in France, one in Dunkirk for metals, the other in Lacq for magnets, refining, the manufacture of battery precursors (cathodes, anodes), training and recycling;
- calls for projects on battery reconditioning, recycling and next-generation batteries under the 4th Future Investment Program, which will complement the 2018 Batteries Plan;
- a roadmap between industry and researchers, including the CNRS and the French Atomic Energy and New Energies Commission (CEA), to launch “industrial demonstrators”, particularly for refining.
The French government has announced the mobilization of a billion euro investment fund to strengthen the resilience of the industrial fabric of metal supply chains.
But governments must also be careful to avoid the risk of overcapacity and carefully weigh the subsidies and aid they provide. The consulting firm Roland Berger recently warned of the possibility of a bubble inflated in part with European tax money, with a risk of bursting in the long term.
There is also a point of attention to be had on the constructive normative part, in order to avoid various incidents and accidents such as electric vehicles catching fire when charging (incidents that have also occurred on telephones (smartphones) and laptops), and on the other hand, at the level of standards by country that can be discriminating, and that can play a protectionist role on the world markets.
Conclusion
In any case, the availability of raw materials and materials refining equipment will remain a bottleneck for the establishment of a secure supply chain for the European battery industry for a long time. Whatever the scenario, Europe, the member states and European car manufacturers must do more to secure raw materials for cells produced in Europe. And developing a battery industry on European soil at breakneck speed is far from solving the problem of the future of Europe’s automotive industry.
Update by Violaine Bugnard (2022). LEPMI and Blue Solutions, to create the battery of tomorrow. Dauphiné Libéré, 23.11.2022.
The Laboratory of Electrochemistry and Physicochemistry of Materials and Interfaces (LEPMI) and the company Blue Solutions, based in
Company Blue Solutions, signed a 5-year renewable partnership in November 2022 to develop a new type of lithium battery
lithium battery.
The Lithium & Interface Laboratory (LI 2 ), which has been set up, will have around 20 researchers under the direction of Professor Renaud Bouchet, a professor at Grenoble INP PHELMA. Its objective is to design a new battery that offers greater autonomy and safety, that can be recharged more quickly and that can be truly recycled, by improving the reversibility of lithium, by understanding the microscopic processes at the interfaces and by reducing the operating temperature of the batteries.
Notes and references
Cover image. [Source: © Usine Nouvelle – https://www.usinenouvelle.com/article/l-europe-veut-ses-batteries-vertes.N681044]
Barrera P. 2021. Batteries Megafactories Surge in Europe as Region Pushes Green Agenda, Investing news INN 24 May 2021. https://investingnews.com/daily/resource-investing/battery-metals-investing/lithium-investing/battery-megafactories-surge-europe-green-agenda/
Beeker E., 2022, Batteries Gigafactories: Europe takes up the challenge. Focus Edenmag°15, 2022 (Energy balance), https://fr.calameo.com/read/005028064579525ec5f62
Fabri Elvire, 2021. REDUCING THE EU’S DEPENDENCE ON CHINESE IMPORTS OF RARE EARTHS AND OTHER STRATEGIC MINERALS in Institut Jacques Delors. BUILDING EUROPE’S STRATEGIC AUTONOMY AGAINST CHINA. Report n° 124. december 2021.chap. 13, p.112-125
Laboué P.dir., 2020. The European battery alliance. European stakes and perspectives. Report n°6 of the Observatory of the security of energy flows and materials. December 2020 https://www.iris-france.org/wp-content/uploads/2021/02/OSFME-R6-Lalliance-europ%C3%A9enne-des-batteries.pdf.
LaplâtreS. 2021. The Chinese recipe for dominating the electric battery sector. Le monde, December 10, 2021
Moores S., 2021, The global battery arms race: lithium-ion gigafactories and their supply chain.Oxford Energy Forum. February 2021: ISSUE 126. p.26-30
Varin Ph. 2022 Report on securing the supply of mineral raw materials to industry. https://www.gouvernement.fr/investir-dans-la-france-de-2030-remise-au-gouvernement-du-rapport-varin-sur-la-securisation-de-l
[1] Giant plants capable of mass-producing products allowing for significant economies of scale